Creating new Sustainability Standards with Closed-Loop Application
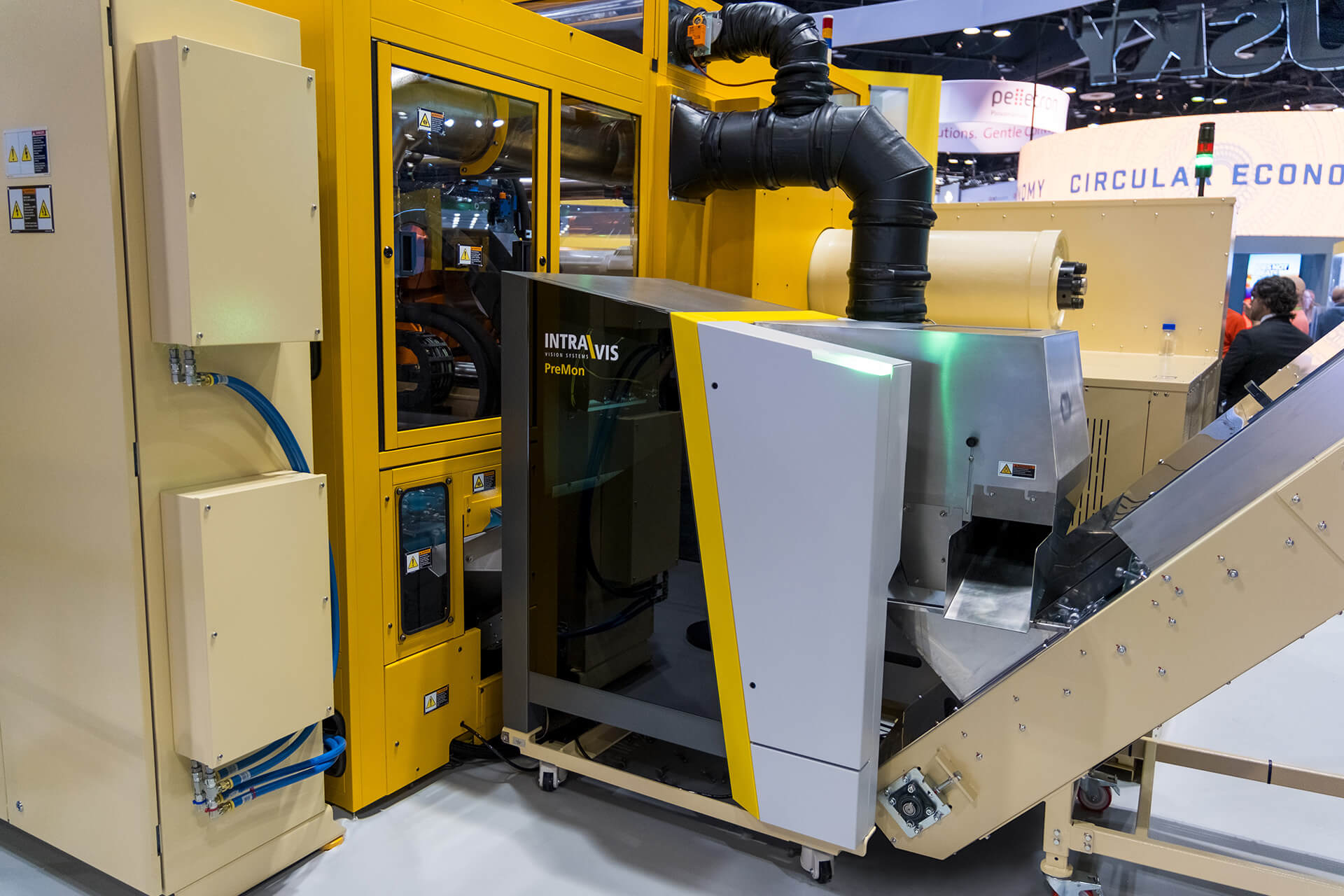
We are happy to announce a pioneering collaboration with Husky Technologies that integrates our preform monitoring system, PreMon, with Husky's HyPET6e platform. This collaboration, demonstrated at the NPE trade show in May 2024, introduces a groundbreaking closed-loop application for rPET preform production, setting new benchmarks in efficiency and enabling the circular economy.
Advanced Closed-Loop Technology
At the heart of this collaboration is the closed-loop application, which revolutionizes color correction in rPET preform production. The solution provides automatic color adjustment to reduce color variability in PET preforms made from recycled content. By using an OPC UA interface for communication, the PreMon and the Husky HyPET6e system work in tandem to monitor and adjust color values in real-time. This integration ensures fast feedback and immediate corrections, with masterbatch automatically added to immediately address any significant yellowing of the preforms. This rapid response capability aims for consistent quality and minimizes waste, enhancing overall production efficiency without the need for operator intervention.
Seamless Integration
premon-command-station-npe-2024-husky-1920x1280px
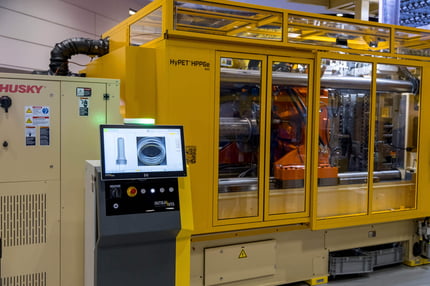
The seamless integration of the PreMon with the HyPET6e system enables direct and continuous feedback on color values. This real-time communication ensures that preforms consistently meet the desired specifications, improving the reliability and quality of the final product. The compact design of the PreMon requires a particularly small footprint in the production hall which leads to significant space savings. The ability to make instant adjustments sets this application apart from traditional methods: It offers a significant advantage in maintaining color consistency and reducing variability.
Driving Circular Economy with rPET bottle production
The collaboration also emphasizes eco-friendly innovation. At NPE, the production of a lightweight preform made entirely from 100% rPET was presented to be blown into a 595 ml bottle. Weighing just 5,89 grams, the preform supports the circular economy using recycled materials without compromising performance. Prioritizing recycled PET is fundamental as it helps reduce reliance on virgin plastics, lowers greenhouse gas emissions, and decreases the amount of plastic waste in landfills and oceans. By reusing existing materials, rPET production conserves resources and energy, contributing to a more sustainable and environmentally friendly manufacturing process. This sustainable approach aligns with global environmental goals and demonstrates the commitment of both companies to enable a circular economy, promoting a more sustainable future for the plastic packaging industry and beyond.
Uncompromising High-Speed Production
The HyPET 400 HPP6e system on display at NPE 2024 was equipped with a 144-cavity, 45-pitch mold running at a cycle time of just 4,5 seconds, achieving a production speed of more than 120,000 preforms per hour. This high-speed capability, complemented by the PreMon, enhances production efficiency, and meets the increasing demands of the packaging industry. Both the HyPET6e system and the PreMon are designed to handle this rapid pace, ensuring seamless integration and continuous, high-quality output.
Detailed quality monitoring beyond color
premon-intravision-in-husky-ui-inline-npe-2024-1920x1280px
Conclusion: Towards Sustainable Manufacturing
The collaboration between Husky and us marks a significant advancement in rPET preform production. By combining cutting-edge technology with a commitment to sustainability and efficiency, this collaboration sets a new standard in the industry. The innovative closed-loop application aspires to drive future developments and improve overall production processes, benefiting both manufacturers and consumers.
Get a brief insight into the closed-loop application of NPE 2024 in the following video:
Get more details about the monitoring system on the PreMon webpage!