More space in production: how the new Tower Hopper saves 40% space
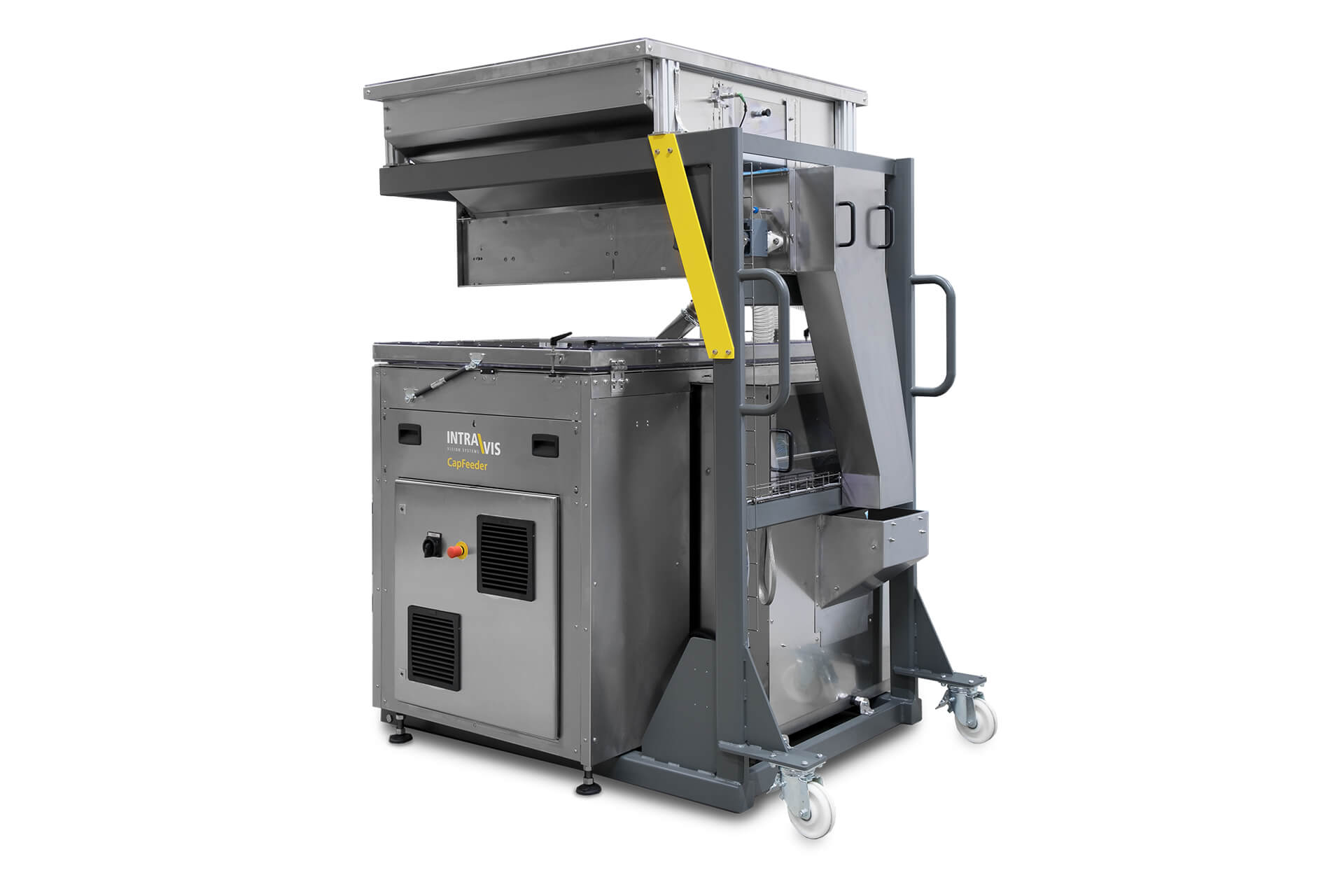
Discover an innovative solution that not only saves space, but also completely rethinks the feeding of closures to the inspection system. Bunker and feeder are combined on a very small footprint – with the same performance as before.
For more than 30 years, INTRAVIS GmbH has been known primarily for its high-quality vision inspection systems for the quality control of plastic packaging. In recent years, however, we have made a name for ourselves with feeding solutions for plastic closures. We launched our first in-house sorter – the CapFeeder – back in 2018. Since then, it has been characterized by the fastest feeding performance on the market.
In the meantime, we also expanded our portfolio of feeding solutions to include cooling and cross conveyor belts, which can be optimally adapted to the respective production line layouts of customers.
We now present a new, compact, and space-saving solution for the feeding area. The so-called Tower Hopper is arranged vertically above the CapFeeder on a footprint of just 3 m². The hopper serves as an intermediate buffer and forwards the closures to the CapFeeder. The CapFeeder orients the closures and transfers them to the inspection system.
Developed for a major customer, this solution addresses one of the largest problems in modern production facilities. Marius Pötting, Product Manager Caps and Closures at INTRAVIS, is responsible for closure inspection systems and therefore also feeding solutions. He reports: "We often hear, especially from our customers in industrialized countries, that they lack space at their production sites. They try to make maximum usage of their production area and eventually reach the natural limits of their premises. With a customer-oriented solution in mind, we have now optimized the space utilization of the feeder by arranging the Tower Hopper vertically above the CapFeeder. This has significantly reduced the footprint. Because: In most production halls, there is sufficient space in terms of height. The result is a space saving of up to 40 % compared to previous layouts.”
The performance of the CapFeeder remains unaffected by the small footprint. In combination with the Tower Hopper, the feeding unit achieves the same feeding speed – this means up to 288,000 closures per hour. With a capacity of 400 liters, even large quantities of closures can be conveyed at highest production speeds. The Tower Hopper measures 2.30 meters in height.
"The Tower Hopper in combination with our CapFeeder offers the same performance in a very small space. The Tower Hopper’s first customer is already very impressed." reports Marius Pötting.
For more information on the Tower Hopper and our other periphery solutions click here.