Special projects – A part of our DNA
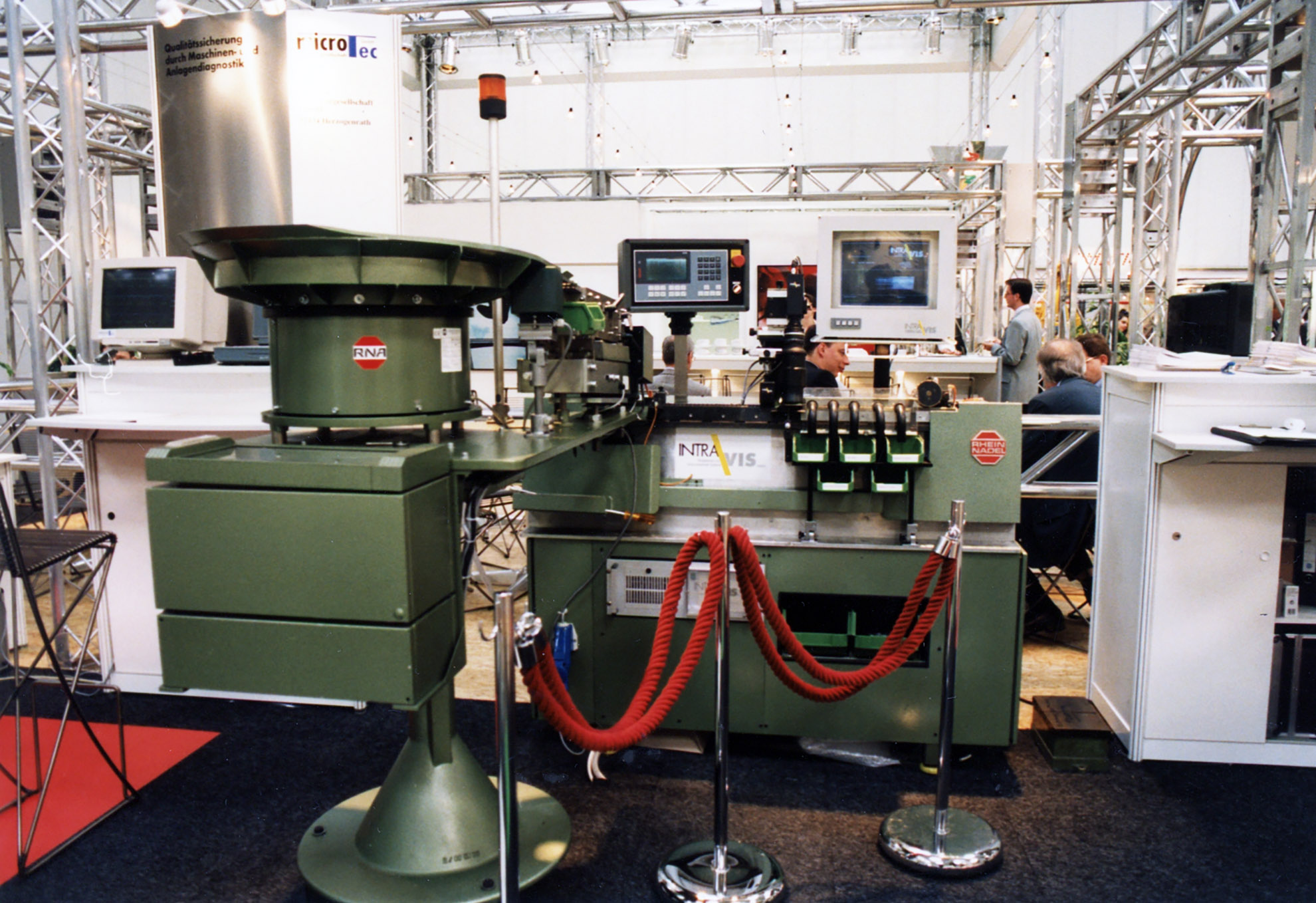
INTRAVIS is renowned for vision inspection systems in the plastic packaging industry. But did you know that, throughout the years, we inspected some rather unusual products, as well? In this blog article, we will introduce you to four of our most unusual inspection systems throughout the last 30 years.
A needle in a haystack
The kick-off for our inspection journey began with a system that holds significant value not only for INTRAVIS but also for the city of Aachen, where our headquarter is located.
Over 30 years ago, Aachen was a hub of the sewing and textile industry. During that time, our CEO Dr. Gerd Fuhrmann met a tech-savvy manager from a large needle factory. The manager challenged him: "Build me a needle inspection system, and if it works, I'll buy another one from you immediately."
And so, the journey began. INTRAVIS developed a system capable of conducting comprehensive inspections, effectively replacing the previous manual needle inspection process.
Although the needle production has completely disappeared in Aachen today, this project marked the beginning of a promising venture. INTRAVIS successfully completed its first major order.
An eyecatcher
Another lighthouse project was an inspection system for eyebrow liners. These products, available in various diameters and formats, must meet the stringent quality requirements of the cosmetics industry.
For this special application, our inspection system employs four side cameras and a top camera to thoroughly inspect the pencils. The key inspection criteria are:
- Pinholes: Detecting dark inclusions to ensure flawless appearance
- Color identity: Verifying the correct shade to maintain color consistency
- Surface defects: Inspecting for contaminations, spalling, and any imperfections
- Tip contour: Ensuring the tip is intact with no protruding or missing material
This comprehensive inspection process guarantees that each eyebrow liner meets the highest quality standards, providing end consumers with reliable and top-notch cosmetic products.
Support during pandemic
During the COVID-19 pandemic, rapid tests were crucial for assessing the risk situation accurately and promptly. Ensuring 100% product safety was vital to prevent contamination or manipulation of these tests by external factors. In 2020, we contributed to the fight against COVID-19 through the effective combination of our CapWatcher Q-Line and Sample-PreWatcher systems for inspecting test kit components.
The Sample-PreWatcher played a critical role in the inspection of the test tubes. It meticulously examined the sealing surface, bottom area, color, gate as well as thread. Additionally, it included cavity number reading and the measurement of geometry to ensure highest quality standards.
The CapWatcher Q-Line focused on inspecting the caps for these test tubes. The system conducted thorough inner and outer inspections, print inspection, cavity number reading, micro-hole inspection, and temperature measurement.
Altogether, millions of test kits were inspected by INTRAVIS systems, and we are proud that we could contribute to the fight against the pandemic.
But first, coffee
And there is another special project with products that many of us get in touch with every day. In 2013, we had a project for the inspection of coffee capsules and their integrated filters. Since then, the inspection system ensures that every coffee capsule meets the highest standards of quality to guarantee a functional and reliable product for the end consumer.
Our inspection system meticulously checks the following criteria to ensure the quality and integrity of each coffee capsule:
- Presence: Ensuring that every capsule contains a filter
- Identity: Verifying the correct inner components
- Positioning: Verifying that the filter is properly positioned within the capsule
- No “dog-ears”: Checking for folded filter areas that can affect performance
- Damage inspection: Detecting any holes or damage to the filter
- Double filters: Identifying and rejecting capsules with double or partially double filters
- Cut-out: Ensuring the filter is correctly cut out on the inner and outer circle
By ensuring these rigorous inspection criteria, the application supports end consumers enhancing their coffee experience to the next level.
Fun Fact: In 2024 this customer asked us to update the systems to the latest software version. So, we can be sure that the capsules will continue to be of the highest quality for the next 10 years.