Part 4: About bottles, closures, decorations and preforms!
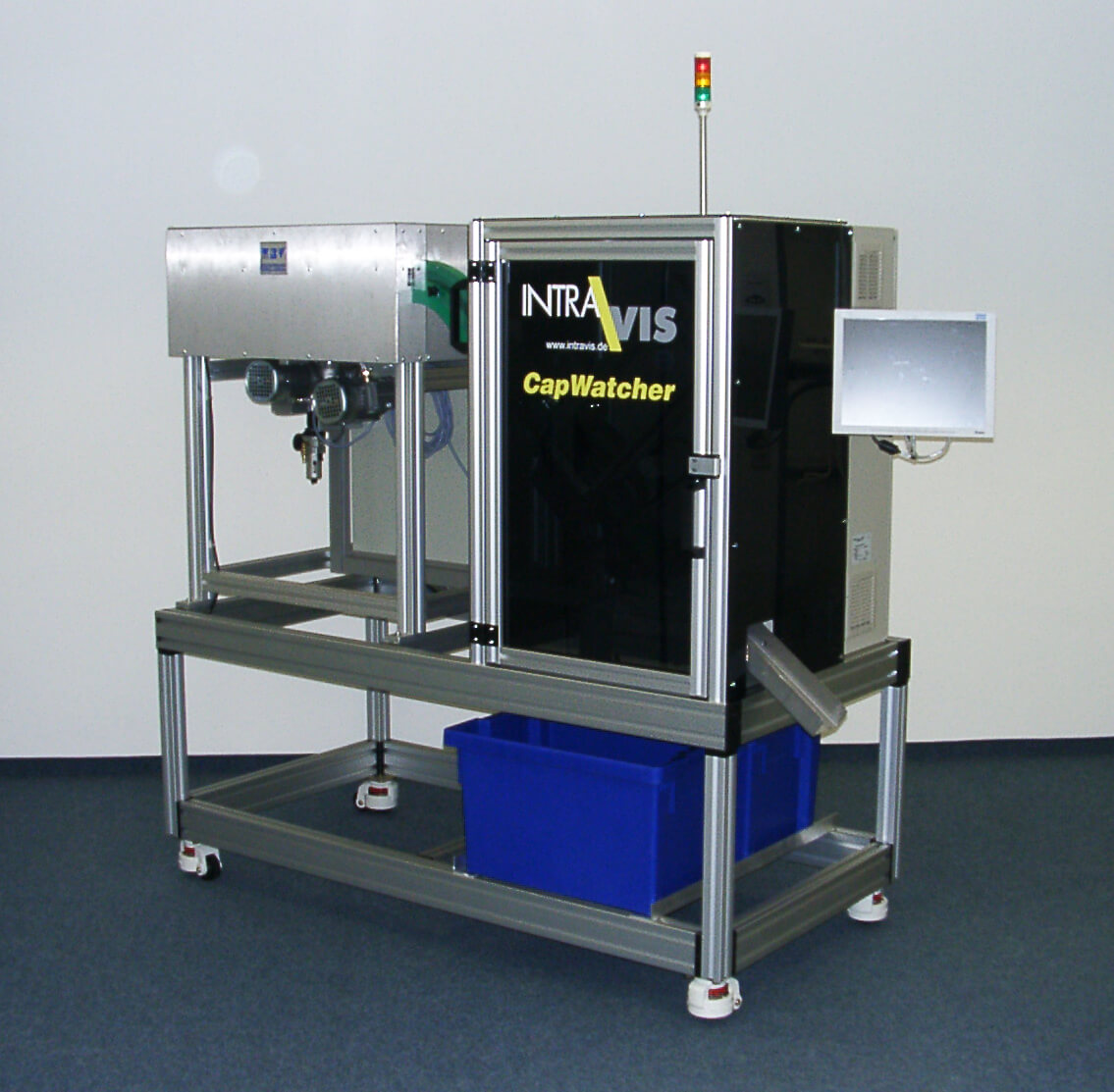
On the occasion of our 30th company anniversary, we look back on the development of INTRAVIS in a 6-part series. We shed light on where it all began, why INTRAVIS is actually called INTRAVIS, what influence a student had on our start in the plastic packaging industry, and how a vision has always driven us for 30 years now. Today: Through the years, we have developed many different systems and technologies. Some of them have accompanied us for more than 25 years.
In the early days of INTRAVIS, we focused on the development of computer tomography devices. Then we switched to CD cases. But we eventually found our true vocation in supplying vision inspection systems for the quality control of plastic packaging. Even if you don't expect it, our solutions are close to people's everyday life. Because: with our systems, we inspect bottles, preforms, closures and labels that millions of people come into contact with every day.
The bottle inspection systems: From the AVI-1 to the tailor-made SpotWatcher Customized
Since we turned our attention to the inspection of plastic bottles with the legendary AVI-1 in 1998, our bottle inspection systems have developed enormously. Even at that time, the inspection scope of our system included defect types such as flashes on the outer rim or in the handle area, geometric characteristics of the neck area, or even inspection for contaminations. It already offered precise object tracking throughout the entire inspection process, so that targeted ejection was possible. The biggest difference to today: At that time, our AVI-1 only managed 3 bottles per second. However, in those days, this still represented an enormous gain in efficiency compared to manual or random inspection in the laboratory.
In 2001, we introduced the successor model AVI-2. The scope of inspection did not change much, but the speed did: from 3 to 7 bottles per second. The success story of our SpotWatchers really took off from 2005 onwards. Over the years, the inspection scope has been extended more and more and the inspection speed has increased to up to 10 bottles per second.
Today, our customers in the bottle sector have both standard systems like the SpotWatcher Basic at their disposal, as well as the option of individually configuring their system based on all their requirements. This is what we call the SpotWatcher Customized, which is increasingly being used in medical applications and cleanrooms.
We started our journey in the plastic packaging industry with the AVI-1
The cap inspection systems: from the CapWatcher to the "quality lab in the production line"
From 2001 onwards, the second area to which we dedicated ourselves was the inspection of plastic closures. We developed our CapWatcher for this purpose, which was already capable of inspecting up to 30 closures per second. The scope of inspection at that time already covered the most important aspects of closure quality: an internal and external inspection to detect contaminations, scratches and notches was just as much a part of it as the inspection of geometric characteristics, the inspection of the guarantee bands and even the search for and detection of micro holes. At that time, this was still done using cameras. From 2007, then already with CapWatcher II, we used a new technology to detect micro holes: a pulsed high voltage inspection, which found even the smallest holes that a camera could not detect.
Through the CapWatcher III, which was launched in 2014, we came to our current systems. Today, our portfolio includes the CapWatcher Q-Line, which is often referred to as the quality laboratory in the production line, the CapWatcher SC for the inspection of specialty closures, the space-saving and cost-effective CapWatcher B-Line, and the CapWatcher FC for the application in the wet area of a production line.
Over the years, we have always used new technologies in our closure inspection systems. For example, the CapWatcher Q-Line uses temperature measurement, which allows the operator to draw conclusions about the shrinkage behavior of his closures, as well as non-contact high-voltage inspection. This removes the need for us to dip into the cap to find micro-holes. In addition, our CapWatcher FC was one of the first systems on the market to detect the application angle of applied caps on bottles.
And the speeds have also almost tripled from 30 closures per second in the past to up to 80 closures per second today.
The decoration systems: from an AVI-1 inspection module to specific label inspection systems
Also in 2001, we decided to transfer our expertise in inspecting labels, which we already had since the AVI-1, into a separate system. This was the birth of the Ilcon 2000, which was already capable of inspecting an impressive 14 labels per second and offered customers the assurance that the right labels were in the right place on the bottle and had neither wrinkles nor bubbles.
The Ilcon 2000 formed the basis for the LabelWatcher, which can still be found in our portfolio today. However, some things have changed over time. Starting with the speed (today we inspect up to 30 labels per second), the range of application of our LabelWatcher has increased. Since last year, the LabelWatcher has also been available in Washdown Design, making it suitable for inspecting labels in the wet area of a filling line. And in 2023, we introduced the LabelWatcher 360°, a label inspection system that can inspect 360° labels on bottles in any rotational position.
However, it has always been clear to us that different types of labels also require special treatment and inspection and that not all of them can be grouped together. For this very reason, we developed the IMLWatcher in 2009, which explicitly focused on the inspection of IML-decorated products. It is one of the few systems on the market that also reliably detects specific IML defects such as short shots or blow-byes.
Since 2022, the SleeveWatcher for the inspection of sleeve-labeled products has expanded our portfolio in the field of decoration and label inspection.
The preform inspection systems: From the PreWatcher to a comprehensive inspection concept
The "latest" area in our company comprises inspection systems for preforms. But after more than 20 years of experience, can we still talk about the "latest area"?
It all began in 2003 with the PreWatcher. It could already be integrated into production lines and inspected up to 7 preforms per second. In addition to inspections that are still considered standard today (e.g. geometry of the preform and its mouth, material defects in the preform body, color inspection), the PreWatcher already offered a technology that can still be found in our systems 20 years later - now in a more advanced form: OCR for cavity number recognition. Already at that time, it helped to sort out preforms that were produced by an incorrectly adjusted cavity. As time went on - the PreWatcher II and PreWatcher III came on the market - we developed another idea: we could no longer just sort out if a cavity was faulty, but we could correlate the large amount of product-related quality data with the specific cavities. This allowed the system to detect when the produced quality of a cavity was declining before the machine operator could, and warn him at an early stage that he must take action. (You can also read more about this in the upcoming part of our series).
Talking about PreWatcher III: Today known as PreWatcher Inline, it represented a major milestone in our history. With it, we were able to offer our customers a combination of sorting unit, feeder, and inspection station on just 8 m² - integrated into the production line directly behind the injection molding machine.
The PreWatcher was supplemented in 2009, 2018 and 2019 by three further systems: the Sample PreWatcher (2009), the PreWatcher Offline (2018) and the PreMon (2019). Today, they all together form our concept for the comprehensive inspection of preforms. For example, customers can perfectly combine the PreMon, our monitoring system in the production line, with the PreWatcher Offline for potential re-sorting in the warehouse. These two are complemented, for example, by the Sample-PreWatcher, which is a high-precision laboratory system that can provide the most accurate inspections and quality reports for submission to your customers.
A PreWatcher from 2003
Excursions into other industries
Of course, in the course of 30 years now, there have been frequent excursions into areas that must still be regarded as special projects. For example, we think back to projects for the inspection of glass, wash pieces or crown corks. A special place is given to our sorting system for asparagus spears, which we have been producing for a well-known agricultural machinery manufacturer for more than 20 years and which is still one of the leading systems on the market today. But also such exotic projects are part of our growth. And with each of these projects, we have been able to gain experience that is still helpful today when implementing new ideas and systems.
In the next part of our series, we will discuss the vision that has guided us since our beginnings and how it began to become a reality in recent years.
Click here for the previous articles in the series:
- Part 1: Die Anfänge der INTRAVIS
- Part 2: Wie wir zu Kunststoffverpackungen kamen
- Part 3: Wir wachsen!